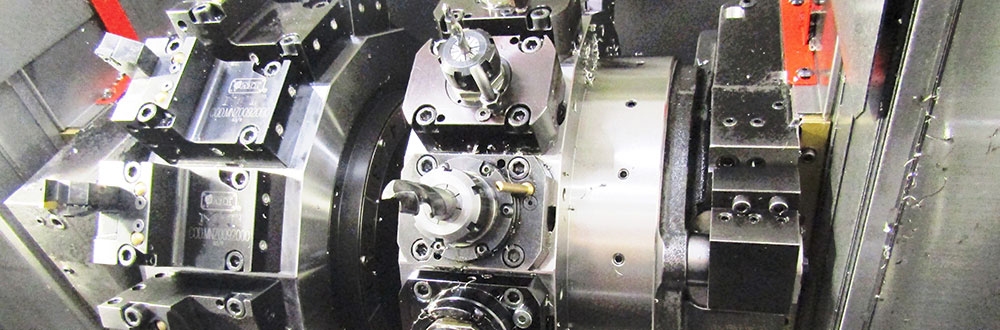
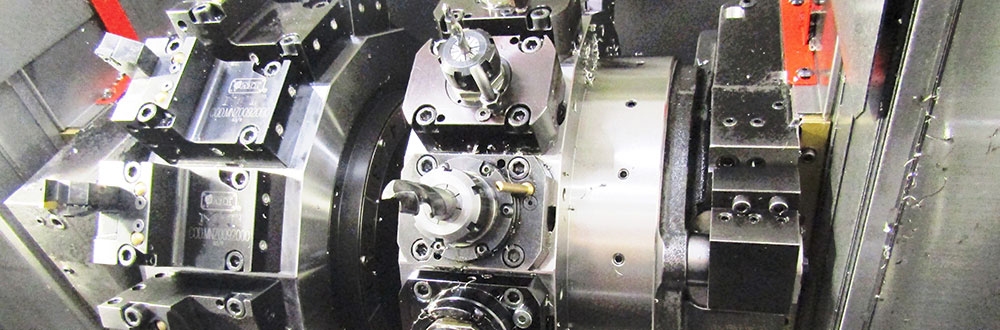
« Metal in the casting process is characterized by forcing the molten state at high pressure into a mold cavity. The main die casting alloys are: zinc, aluminum, magnesium, copper, lead and tin ».
When a manufacturer of die-casting or injection molds receives a request from his customer, they project the mold and thus meet the requirements of the drawing in object. Yet this answer, not always, is the most effective since it aims only at the geometric adhesion of the piece.
To produce by die-casting process involves multiple aspects which may be preliminary to the production itself; to draw up an activity made by steps foresees an acquaintance of the product and the process, of their interaction during the molding phase. With the help of tools such as casting and process simulations, it is easier for the operator to reach the desired result: a product burr free and almost without porosity.
It is not innovative the process that leads to the result, what is innovative is the activity of calibrating all these technical aspects, so as to get a part which we call in conformity with the drawing. Looking further, what comes out to be essential is to optimize the process so as to make it efficient and economical for the user, therefore competitive.